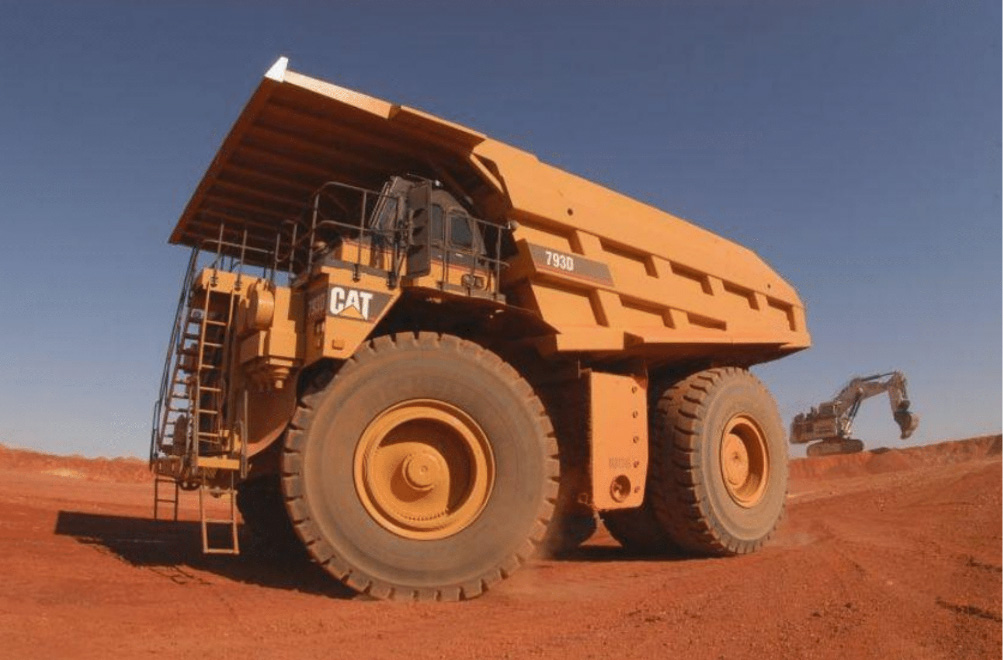
Terrestrial Mining Project Development Sequence
Terrestrial Mining Project Development sequence ; and thoughts for asteroid mining ventures
Terrestrial project planning goes something like:
Target generation:
Discovery of Mineralization:
Quantification investigations
Announcement of Mineral Resource (per JORC or 43-101)
Metallurgical test work and Flowsheet development
Conceptual Mine Plan
Conceptual costings: Scoping Study
Preliminary Feasibility Study (PFS) and Statement of Ore Reserves
Definitive / Final /Bankable Feasibility Study (DFS / BFS / FFS)
Board Approval: Award of EPC contract (Engineer-Procure-Construct)
Commission: and finally Operational /First Deliveries.
If you are really lucky, and have planned and managed with extreme discipline and caution, your project then finally comes on line with more-or-less its intended ‘nameplate’ capacity and more-or-less on budget and on-time. But commissioning can be a long and harrowing process.. that can sometimes require substantial rebuild (euphemistically, ‘debottlenecking’)of the (still new) mine and /or plant..
The Studies Sequence for Risk-reduction and Capex clarification
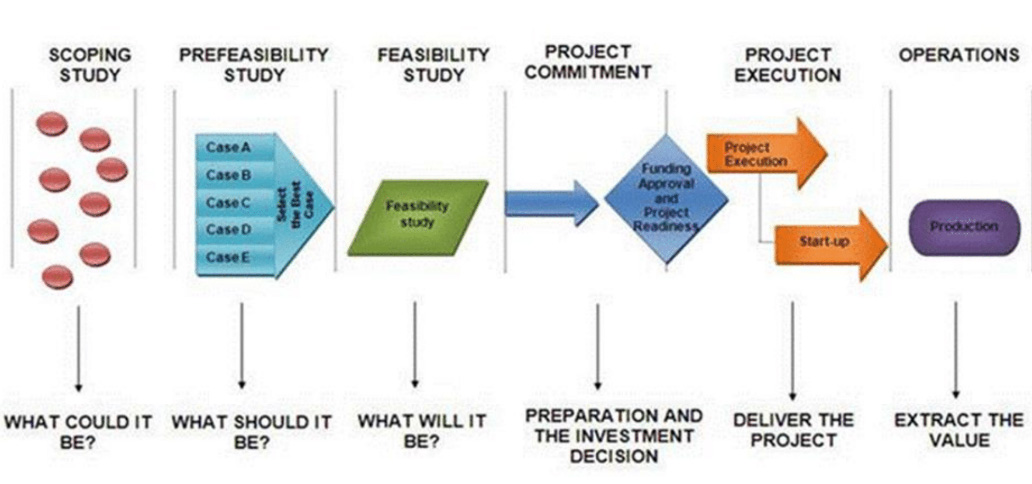
Key mining and metallurgical parameters are grade and recovery. ‘Grade wins’, as high grade will forgive poorer than expected recovery.
Key financial numbers are Capex, Opex, breakeven $/kg of product, Payback Period, NPV.
Bench Tests, Test pit, Trial Mine, Pilot Plant: Just how much risk-reduction (a) do you need?-and (b) can you afford
At Olympic Dam, we spent 6 years on pre-approval underground trial mining / mine development, and spent (IIRC) $50M on a very large Pilot Plant that ran in two extended campaigns over most of 2 years.
Minimum Viable Project (‘Demo’ Plant, perhaps?)-to prove process / capture market.
The ‘Uniqueness’ of each mining project: Different mining methods, extraction processes, and logistics challenges. Mining projects are generally Not Cookie-Cutter projects…
Neither will be our asteroid targets.
Grade:
For gold mines, it’s ounces per ton, or grams per tonne (identical to parts per million, ppm). Most surface gold mines have an economic cutoff at about 1 ppm. For underground mines, cut off depends critically on depth and on mining method (stopping method),and on on going development cost, often described in terms of $ per metre vertical depth versus ounces per vertical depth
For uranium mines, grade is expressed in lb of U3O8 per ton, or kg/tonne, or %.
For copper mines, it’s % Cu.
But really, in all cases, it’s actually $/tonne.
For asteroid mining, seeking to recover water, grade will be in % H2O, of course. But the valuation will depend on where it will be delivered to. It is going to be most important to find out what we will be earning ($/kg) for our product in(a) GEO and (b) LEO, and (c) HEEO and EM L1 / Gateway.
Development / Capex costs:
Terrestrial mining projects face massive upfront capital costs and long development times (just like space mining ventures, perhaps) Open pit pre-strip (or, if an underground mine, head frame construction /winder installation, shaft-sink, and underground development to access orebody); construction of mill / concentrator / beneficiation plant, and tailings dam; construction of supporting infrastructure (powerplant, wellfields, air strip, accommodation camp, road or rail link to port, etc.).
Note that some of these cannot be scaled down proportionally if scaling down the project throughput. (eg airstrip has to be a certain minimum length, road has to cost $x per km)
Time for pre strip or for shaft sink and U/G development, for example, cannot be magically foreshortened. (Bit like the time constraints the space miners will have imposed by Hohmann Transfer transit times)
Just as an aside, shaft-sinking is unbelievably tedious, time-consuming and expensive. At Olympic Dam, in the 1980-81 period, whilst watching the slow vertical progress, I was drawn to compare it with the immense effort to get stuff into orbit to construct a space station…Once the shaft is to target depth, and initial (house sized) ‘plat’ opening is cut, then you have to disassemble the first basic equipment (front-end loader, jumbo drill, and truck) and carefully lower them half a kilometre or more down the shaft to that initial hand drilled underground opening from which they will work outwards, and there in the mud, reassemble them and get them running.. Quite a bit like building a space station..